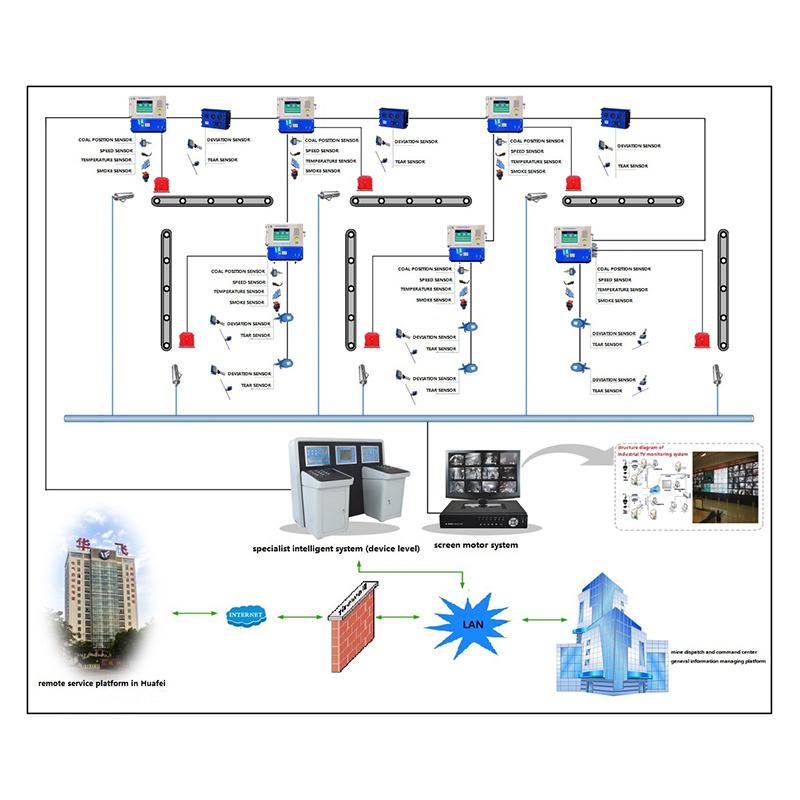

Belt Conveyor System
The Solution of Conveyor System Based on Intelligent Mine
Application Scope
The solution integrates intelligent control of the belt conveyor system, telephone dispatching and video monitoring to build a complete dispatching, operation and monitoring network system. It can not only improve equipment safety production efficiency, save resource consumption and reduce operation personnel, but also realize unattended belt conveyor system and intelligent system operation. It is suitable for the comprehensive requirements of intelligent control and management upgrade of underground and surface belt conveyors and their related subsystems, and is a tailor-made solution for high-end customers who have requirements for unattended system and intelligent operation of mines.
Main characteristics
The solution takes the safety,reliability and intelligence level of intelligent control of the conveyor system as the core, and can provide real-time monitoring, fault warning,data and information teleportation and storage,invisible fault intelligent analysis and other specialized processing of key information of the main equipment and process control of the conveyor system. It realizes intelligent functions such as self-diagnosis, fault warning and invisible fault warning at the equipment and system levels,and supports the uploading of management information and the transmission of control commands. The intelligent "system plug-in" function can easily realize information interaction with other information systems and meet the needs of intelligent mine implementation and operation at low cost.
“5+1+2”Intelligent Control Solutions for Conveyor Systems
This solution is divided into two sets of solutions from the use of environmental considerations, underground and surface, the main difference between the two sets of solutions in the use of equipment caused by the environment of explosion-proof and protection level, the other main control functions and performance are basically the same.
“5+1+2"The solution includes conveyor automation control system,conveyor energy management system,conveyor expert intelligence system (equipment level), audio communication system, video monitoring system,network communication and data remote transmission channel, scheduling management and monitoring platform,remote service platform with five subsystems, one channel and two support platforms.
1.Conveyor Automation Control System
The conveyor automation control system takes the high performance PLC as the core control device,and the single belt conveyor control takes the embedded single chip microcomputer as the core control device. The whole system runs in the high efficiency and low consumption mode of "start with cal stop without coal fast with more coal, slow with less coal ", which has the characteristics of advanced technology, stable performance,safe and reliable,good economy and low energy consumption. By collecting and processing the working condition nformation of each sensor in real time, the operation condition of the equipment is accurately judged,it also has the functions of communication, control,protection, fault location,animation display and voice alarm.It can meet different special control and communication requirements at user site.
2.Conveyor Energy Consumption Management System
The actual load of each conveyor belt is acurately measured through professional and reliable detection and a complete set of the intelligent control algorithms. Taking the belt conveyor system as a whole, the system adjusts the running speed of each belt machine, so that it runs in the high efficiency mode of "start with coal, stop without coal, fast with more coal, slow with less coal" .
3.Conveyor Expert Intelligent System (Equipment Level)
Mainly include: harndware facilities of industrial control computer, displayer, special collection card, communication network, as well as appication software packages of monitoring software expert think tank. The main software function modules include equipment management module, equipment condition monitoring module,fault information management module, system condition reproduction module, expert think tank module, remote diagnosis module.
4.Audio Communication System
The voice call requirements along the conveyor line are easily solved through the intrinsically safe amplifying telephone (including emergency stop) installed along the system.
5.Video Surveillance System
Load point, transfer point, unloading point,crusher,coal bunker,workstation and other place needs monitoring.
6.Network Communication and Data Remote Transmission Channel
The signal is transmitted to the dispatching command center through LAN to provide hardware and software interface support.
7.Dispatching Management and Monitoring Platform
If the dispatching system has application software, data interaction can be carried out directly after shaking hands approved by both parties. If there is no application software, the application software can be provided torealize the application requirements.
8.Remote Service Platform
Remote service platform support system (Locate in Jiaozuo, Henan Province, serving all customers): based on reliable network security mechanism support to achieve remote diagnosis of equipment and other intelligent functions through the public network. Remote detection and high-quality service is available for mine hoist, belt conveyor,main ventilator and other large mine equipment.
Main Function Module Introduction of "Expert Intelligent Software System" in Conveyor System
Module 1 "Equipment Conditions Monitoring Module"
To detect at real-time, record and monitor the working condition of the system equipment in the field through safe and reliable technical means, and the state information of the equipment is displayed in a dynamic and intuitive way.
1) Medium and low voltage power supply equipment: Voltage,Current, Power, Power Factor, fault information.
2) Motor drive equipment (VFD and speed regulation device): Voltage,Current, Power, Power factor, fault information, etc.
3) The three-dimensional mechanical vibration,noise,bearing temperature of motor, gearbox, drum and other main mechanical and electrical equipment, wire rope operating conditions;
4) Lubrication station, hydraulic station and brake control: brake oil pressure, pressure difference, oil temperature, oil quality, lubricating oil temperature, brake clearance, brake fatigue and brake swing, etc.5) Information monitoring related to hoisting process : container position,running speed,speed diagram, torque diagram, signal status,running direction,forward and reverse to correct place,acceleration and deceleration information.
Module 2"System Condition Recurrence Module"
This module is the front module of the system expert think tank. According to the need of problem analysis, the user can select operation condition recurrence of a single or Multi- equipment at the corresponding fault time. This function greatly facilitates the analysis of the cause of equipment failure, helps to find the reason,and eliminate the deep causes in the equipment and management.
Module 3 "Fault Management Module”
This module mainly focuses on statistics, classification,summarization and in-depth analysis of fault and potential fault information existing in equipment operation,and comprehensive analysis and judgment with the help of expert experience or previous problem handling experience. It provides support to realize the intelligent operation,fault diagnosis,and troubleshooting of the upgrading system. The system assists maintenance personnel in locking out fault phenomena,analyzing fault causes, and guiding troubleshooting.
Module 4"Precision Maintenance Module”
To ensure the safety performance of the hoist system, the user should conduct relevant protection tests and equipment maintenance inspections on a daily basis according to the regulations. The system can quantify and monitor the hidden dangers of the main equipment according to the actual operating condition of the equipment each shift,and warn the equipment amount parts with excessive indicators for daily maintenance, key maintenance and enhanced maintenance distribution. Automatically remind the maintenance personnel to check and deal with in time,and the system automatically records the results of problem ranking.
Module 5 "Self-diagnosis Module”
Expert think tank has a three-level self-diagnosis function of sensor self-diagnosis, major equipment self-diagnosis and hoisting system self-diagnosis set up according to different configurations of on-site equipment. Improved system reliability and potential fault prediction capability.
Module 6"Equipment Management Module "
Establish equipment files, overhaul and daily maintenance information, and provide accurate maintenance guidance throughout the entire life cycle of the equipment.
Main features of expert intelligence software system
4、The system is based on the full coverage of sensor sensing of hoisting equipment, which can realize a series of intlligent functions such as unmanned operation and controlof hoit,intligent video monitoring. elevator cagefeeling accurate maintenance, remote technical support, and automation of monitoring and management, greatly improving the safety and reliability of the system.
2、Based on a reliable and flexible network communication framework, the system can realize self-diagnostic functions at the sensing layer,control layer and execution layer of key equipment. Support advanced operation requirements such as mine hoist unattended, remote control,remote monitoring, remote technical support and emergency drive.
3、The system is equipped with intelligent visible light and thermal imaging video monitoring sotware and hardware facilities, which can monitor the surface temperature of the equipment in a non-contact manner and detect any foreign objects into the area,etc.
4、It has the ability to conduct in-depth comprehensive analysis and specialized processing of equipment working condition data,which can accurately judge the operation condition of system equipment and predict the potential failure of major ecquipment.Can provide comprehensive equipment meaintenance waning information, improve equipment maintenance targeting and significantly recduce equipment failure downtime.
5、Withsensor sel-diagnosis,equipment sel-ciagnosis,and system self-diagnosis functions, remote technical support and troubleshooting are available.
6、The cell phone APP can be used to get to know the operation status of the equipment, which is convenient for the operators and managers to know the operation status of the equipment in time; equipped with Ethernet,RS485,CAN, MODUBUS and other rich communication interfaces,making it easy to transmit data remotely.
Main Console of Intelligent Belt Conveyor
Characteristics: Intelligent belt conveyor main console is the core control equipment of the system. The equipment adopts a PLC with advanced technology and reliable performance,and perfectly handles all the transportation process requirements.'The running status display adopts a 10.4-inch color LCD screen.The system has the function of remote networking, which can transmit all kinds of running states ofconveyor to the dispatching room for monitoring and reliable.
KTC197 Conveyor Communication System
Overview :
KTC197 conveyor communication control system is applicable to mines with explosive gas(methane) and coal dust, and can be used in comprehensive mining and comprehensive excavation workings to realize centralized control and protection of underground coal mining and transportation systems such as down-slot, scraper conveyor and belt conveyor.
The system host takes high-performance PIC as the main control unit of the control system, collects and processes information of various sensors in real time,realizes the functions of communication, control, comprehensive protection,call along the line,fault location, animation display and voice alarm of the whole system, and has rich communication interfaces such as RS485,CAN and Ethernet, which can meet the special communication requirements of different customer sites.
Configuration Solutions
Electric Control System of Belt Conveyor
(1) This conveyor control system can be adapted to the control of a single belt to a whole belt transport line, from a simple"一" transport line to a"丁" or "山" shaped transport line.
(2) One host in the system can control multiple belt conveyors simultaneously. The system can be extended up to 5 km without relay and up to 20 km with additional relays.
(3)The working status and parameters of all equipment along the system line can be displayed and uploaded to the dispatching room through one mainframe,where centralized display and control can be performed.
Electrical control system of comprehensive excavation workings
The system can not only realize centralized control of crusher,reversed loader, transporter and pump station in the comprehensive mining working but also realize distributed control through CAN bus communication.
Diagram of electric control system of belt conveyor
Electrical control system of comprehensive excavation workings diagram